


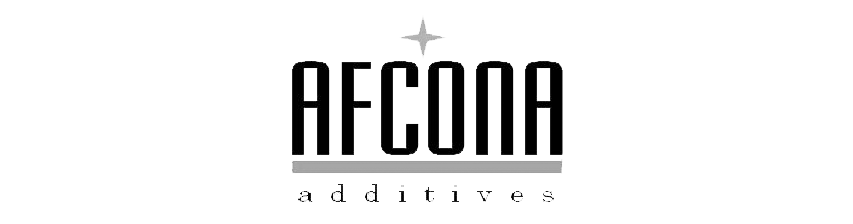
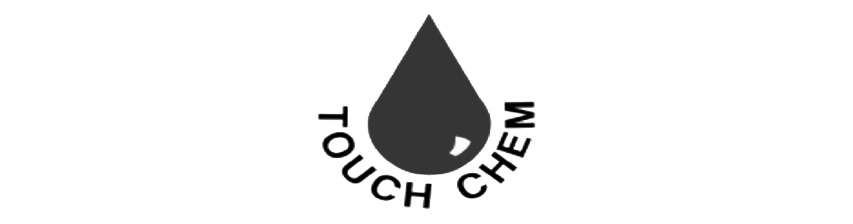



For Universal Pigment Concentrate
Silicone, Pure Acrylic Polymer
As Well As Fluorocarbon
Modified Polyacrylate Polymer
Silicone And Silicone Free
Conductivity Addutive / Anti Static Agent
Anti Gelling Agent
And Many More
For Universal Pigment Concentrate
Silicone, Pure Acrylic Polymer
As Well As Fluorocarbon
Modified Polyacrylate Polymer
Silicone And Silicone Free
Conductivity Addutive / Anti Static Agent
Anti Gelling Agent
And Many More
Cover Solvent Smell With Permanent Fruity Smell
Improve Paint Film Hardness
Cover Solvent Smell With Permanent Fruity Smell
Improve Paint Film Hardness
As Pigment Spacer
White Pigment Alternative
As Pigment Spacer
White Pigment Alternative